The power system includes elements:
- fuel supply system, which includes a fuel tank, an electric fuel pump module, pipelines, hoses, a fuel rail with nozzles and a compensator for fuel pressure pulsations;
- air supply system, consisting of an air filter, an air supply hose and a throttle unit;
- fuel vapor recovery system, including an adsorber, an adsorber purge valve and connecting pipelines.
The functional purpose of the fuel supply system is to ensure the supply of the required amount of fuel to the engine in all operating modes. The engine is equipped with an electronic control system with multipoint fuel injection. In a distributed fuel injection system, the functions of mixture formation and metering of supplying the fuel of the air mixture to the engine cylinders are separated: the injectors carry out a metered injection of fuel into the intake pipe, and the amount of air required at each moment of engine operation is supplied by the throttle assembly. This control method makes it possible to ensure the optimal composition of the combustible mixture at each specific moment of engine operation, which allows you to obtain maximum power with the lowest possible fuel consumption and low toxicity of exhaust gases.
A feature of the injection system of the Toyota Corolla is the synchronization of the injectors in accordance with the valve timing (the engine control unit receives information from the phase sensors). The controller turns on the injectors in series, and not in pairs, as in asynchronous injection systems. Each injector is activated after 720 ° crankshaft rotation. However, in starting modes and dynamic modes of engine operation, an asynchronous method of fuel supply is used without synchronization with the rotation of the crankshaft.
The main sensor for ensuring an optimal combustion process is the exhaust gas oxygen concentration sensor (lambdaasond). It is installed in the exhaust manifold of the engine and, together with the electronic unit and injectors, forms a circuit for adjusting the composition of the fuel of the air mixture supplied to the engine. According to the sensor signals, the engine control unit determines the amount of unburned oxygen in the exhaust gases and, accordingly, evaluates the optimal composition of the air-fuel mixture entering the engine cylinders at each time. Having fixed the deviation of the composition from the optimal 1:14 (respectively, fuel and air), which ensures the most efficient operation of the catalytic converter of the exhaust gases, the control unit changes the composition of the mixture using injectors.
The vehicle has two oxygen concentration sensors: the first is in the exhaust manifold, and the second is after the catalytic converter.

The first sensor is control (based on its signal, the ECU corrects the fuel supply), and the second is diagnostic (according to its signal, the ECU evaluates the efficiency of the catalytic converter).
The fuel tank is made of polymeric material, installed under the floor of the body at the rear and secured by four bolts.
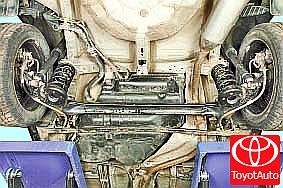
To prevent fuel vapors from entering the atmosphere, the tank is connected by a pipeline to the adsorber of the fuel vapor recovery system. A fuel module is installed in the flange hole in the upper part of the tank, which includes a fuel filter, an adsorber, a pump and a pressure regulator. On the left side of the tank, there are nozzles for connecting the filling pipe and the ventilation hose. From the fuel module, fuel is supplied to a fuel rail attached to the engine intake pipe. From the rail, fuel is injected by injectors into the engine intake pipe.
The fuel lines of the power system are tubes that connect the various elements of the system.
The fuel pump module contains an electric pump.
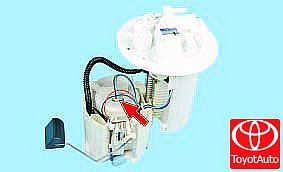
Fuel pressure control.
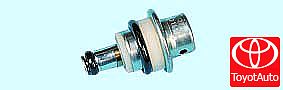
Adsorber.
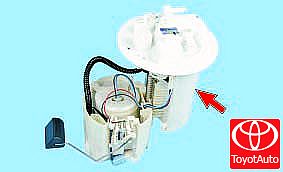
Mesh filter.
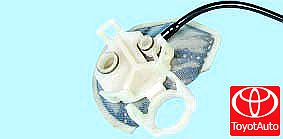
Fuel level indicator sensor.
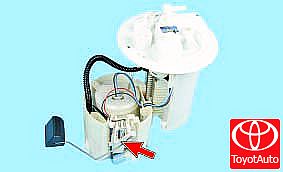
The fuel pump module provides fuel and is installed in the fuel tank, which reduces the possibility of vapor lock since fuel is supplied under pressure rather than under vacuum.
Submersible fuel pump with electric drive, rotary type, with a mesh filter-fuel receiver is a part of the fuel module. The module is installed in the fuel tank, which reduces the possibility of vapor lock, since the fuel is supplied under pressure and not under vacuum. The fuel pump supplies fuel from the fuel tank through the fuel line to the fuel rail at a pressure of 304–343 kPa. The pump of a non-separable design cannot be repaired; if it fails, it must be replaced.
The fuel rail 1 for injectors is a cast hollow part with holes for installing injectors 2 and with a supply connection for connecting a high pressure fuel line. The injectors are sealed in their seats with rubber rings 3.
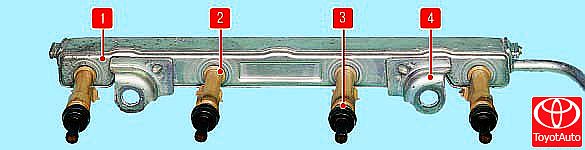
The ramp with the complete injectors is inserted by the injector shanks into the holes of the intake pipe and secured through the lugs with two bolts. The injectors are attached to a ramp, from which fuel is supplied to them, and with their nozzles they enter the openings of the intake pipe.
In the openings of the rail and the inlet pipe, the injectors are sealed with rubber O-rings A and B.
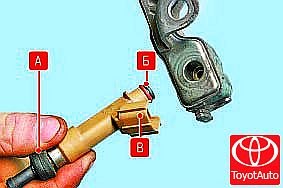
The injector is designed for metered injection of fuel into the engine cylinder and is a high-precision electromechanical valve. Pressurized fuel flows from the rail through channels inside the nozzle body to the shut-off valve. A spring presses the check valve needle against the tapered bore of the gun plate, keeping the valve closed. The voltage supplied from the engine control unit through the electrical connector B to the injector solenoid winding creates a magnetic field in it, which pulls the core together with the check valve needle inside the electromagnet. The tapered annular hole in the atomizer plate opens and fuel is injected through the diffuser of the atomizer body into the intake port of the cylinder head and further into the engine cylinder. After the termination of the electric pulse, the spring returns the core and the needle of the shut-off valve to their original state - the valve is locked. The amount of fuel injected by the injector depends on the duration of the electrical impulse.
The fuel pressure regulator maintains a constant fuel pressure in the engine supply system at all engine operating modes.
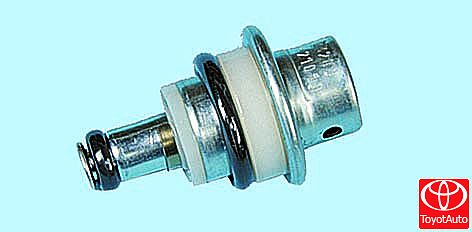
The supply of the electric fuel pump is greater than necessary to ensure the system is operational. Therefore, when the engine is running, part of the fuel is constantly drained into the fuel tank thanks to the pressure regulator.
The air filter is installed on the left side of the engine compartment on a special bracket.
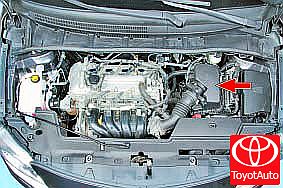
Non-woven filter element, flat, with large filter surface area. The filter is connected by a rubber corrugated air supply hose with a throttle assembly.
The throttle assembly, which is the simplest control device, serves to change the amount of main air supplied to the engine intake system, is installed on the inlet flange of the intake pipe and fastened with screws.
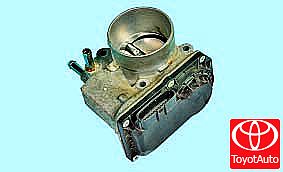
A molded rubber sleeve is put on the inlet pipe of the throttle assembly, secured with a clamp and connecting the throttle assembly to the air filter. The throttle assembly includes a throttle position sensor and a stepper motor for controlling the throttle. There is no mechanical connection between the throttle assembly and the throttle pedal. The so-called electronic throttle pedal transmits information about the degree of pressure on the pedal to the electronic engine control unit, which, in turn, taking into account the vehicle speed, gear engaged, engine load and engine speed, opens the throttle to the required angle.
Source: http://toyotauto.net/corolla/osobennosti-konstrukcii-sistemy-pitaniya.html

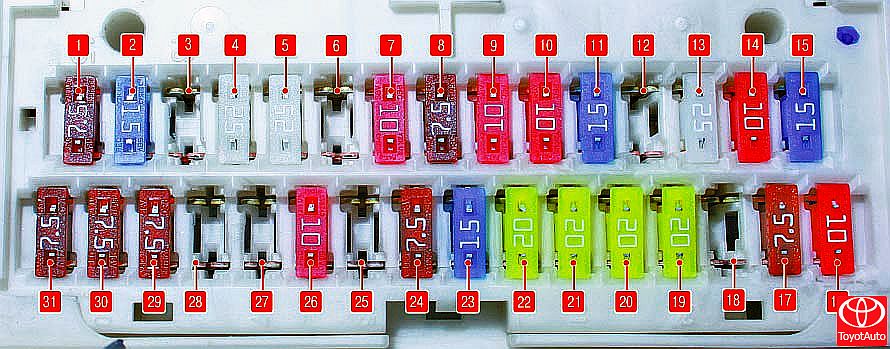
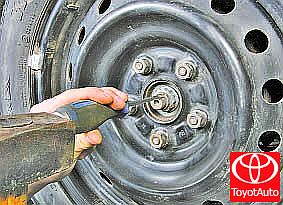
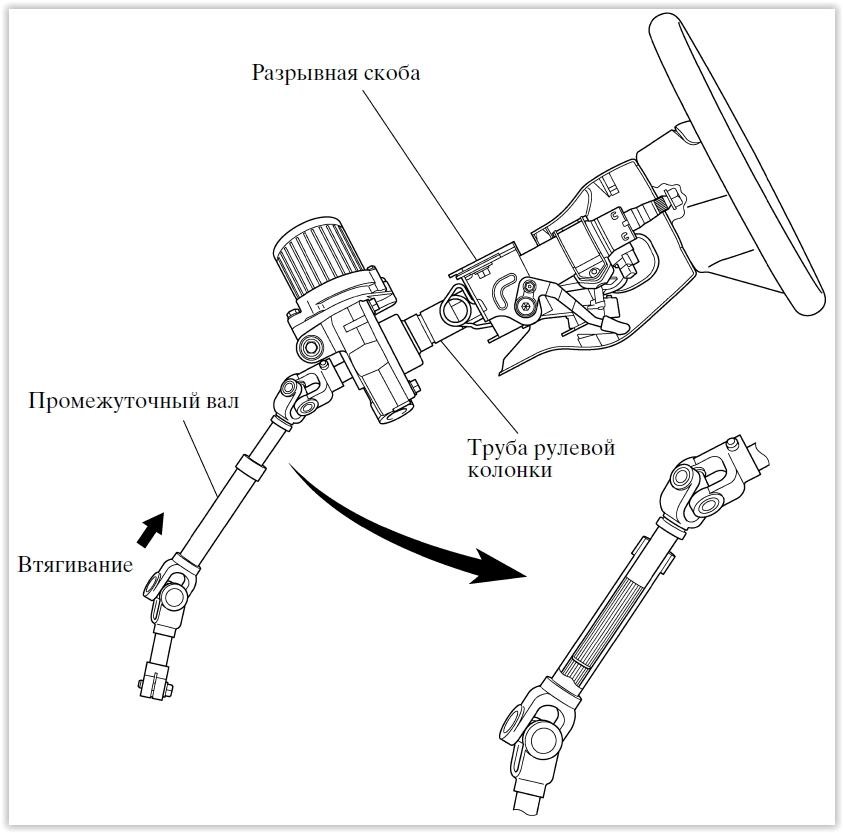
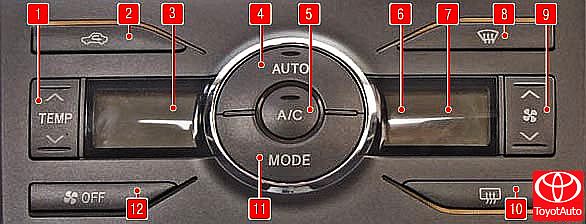
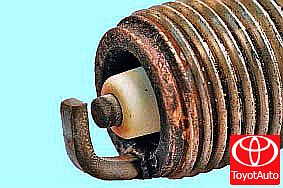
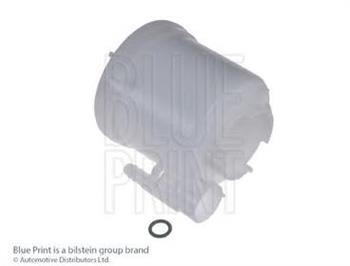
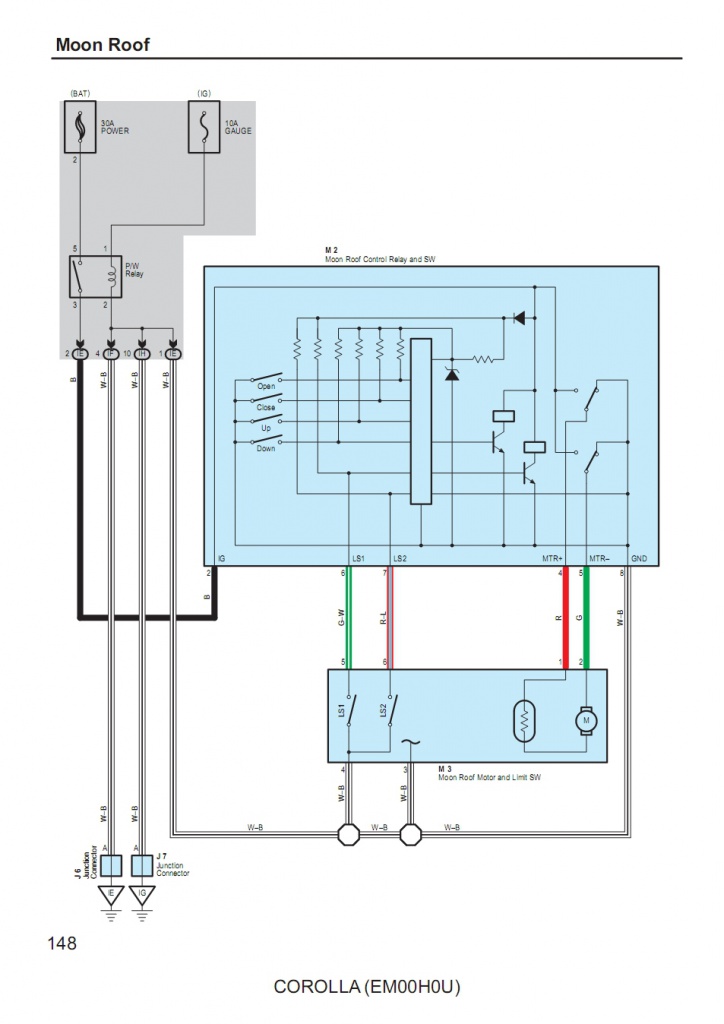
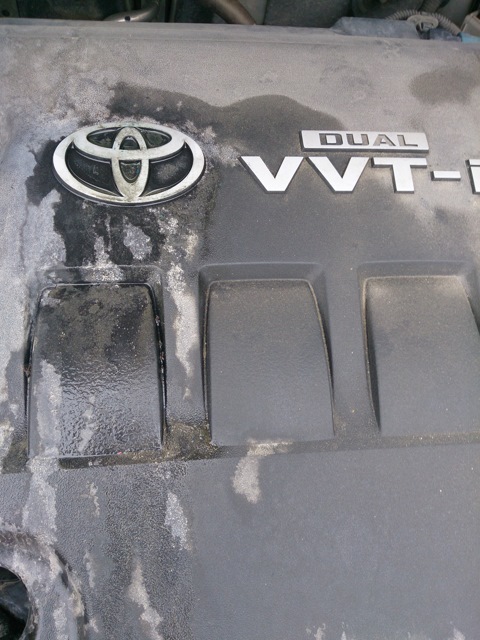