The K7J and K7M engines are identical in design and differ only in displacement. The K7J engine has a displacement of 1.4 liters, while the K7M engine has a displacement of 1.6 liters. The increase in working volume is obtained due to the larger crank radius of the crankshaft and, consequently, the larger piston stroke.
Both engines are gasoline, four-stroke, four-cylinder, in-line, eight-valve, with an overhead camshaft.
Warning: Cylinder firing order: 1-3-4-2, counting from the flywheel.
Power system - distributed fuel injection (Euro 4 toxicity standards).
Engine (front view in vehicle direction):
1 - air conditioning compressor;
2 – a belt of a drive of auxiliary units;
3 - generator;
4 - power steering pump;
5 - oil level indicator (oil dipstick);
6 – a cover of a head of the block of cylinders;
7 - ignition coil;
8 - tips of high-voltage wires;
9 – a head of the block of cylinders;
10 - thermostat housing;
11 - exhaust manifold;
12 – a pipe of the pump of a cooling liquid;
13 - low oil pressure indicator sensor;
14 - technological plug;
15 - flywheel;
16 - cylinder block;
17 - oil pan;
18 - oil filter
The engine with a gearbox and clutch form a power unit - a single unit, fixed in the engine compartment on three elastic rubber-metal bearings. The right support is attached to the bracket on the top cover of the timing belt, and the left and rear support to the gearbox housing.
On the front of the engine (in the direction of vehicle movement) are located: exhaust manifold; oil filter; low oil pressure indicator sensor; coolant pump inlet pipe; spark plug; generator; power steering pump; air conditioning compressor.
Power unit (rear view in the direction of the vehicle):
1 - gearbox;
2 - crankshaft position sensor;
3 - inlet pipeline;
4 - absolute air pressure sensor in the intake manifold;
5 - intake air temperature sensor;
6 - throttle assembly;
7 - idle speed regulator;
8 - oil filler cap;
9 - fuel rail;
10 - oil level indicator (oil dipstick);
11 – a head of the block of cylinders;
12 – block of cylinders;
13 – a belt of a drive of auxiliary units;
14 - oil pan;
15 - knock sensor;
16 – support bracket of the inlet pipeline;
17 - starter;
18 - vehicle speed sensor
Behind the engine are located: intake pipeline with absolute pressure and intake air temperature sensors; throttle assembly with throttle position sensor and idle speed controller; fuel rail with injectors; knock sensor; starter; oil level indicator.
On the right is the coolant pump; timing gear and coolant pump drive (toothed belt); drive of auxiliary units (poly V-belt).
On the left are: flywheel; thermostat; crankshaft position sensor; coolant temperature sensor.
Top - ignition coil; oil filler neck.
The engine cylinder block is cast iron, the cylinders are bored directly in the block.
In the lower part of the cylinder block there are five crankshaft main bearing supports with removable covers, which are attached to the block with special bolts. The holes in the cylinder block for the bearings are machined with the covers installed, so the covers are not interchangeable and are marked on the outer surface to distinguish them (the covers are counted from the flywheel side). On the end surfaces of the middle support, sockets are made for thrust half rings that prevent axial movement of the crankshaft.
The shells of the main and connecting rod bearings of the crankshaft are steel, thin-walled with an anti-friction coating applied to the working surfaces. Crankshaft with five main and four connecting rod journals. The shaft is equipped with four counterweights cast integrally with it. The counterweights are made on the continuation of the "cheeks" of the engine crankshaft. Counterweights are designed to balance the forces and moments of inertia arising from the movement of the crank mechanism during engine operation. To supply oil from the main journals to the connecting rods, channels are made in the necks and cheeks of the shaft.
At the front end (toe) of the crankshaft are installed: an oil pump drive sprocket, a timing gear drive pulley (timing) and an auxiliary drive pulley. The toothed pulley is fixed on the shaft with a protrusion that fits into the groove on the crankshaft toe and prevents the pulley from turning. Similarly, the auxiliary drive pulley is fixed on the shaft.
Flywheel:
1 - crown for the crankshaft position sensor;
2 - a crown for starting the engine
A flywheel is attached to the flange of the crankshaft with seven bolts. It is cast from cast iron and has a pressed steel crown for starting the engine with a starter. In addition, a ring gear for the crankshaft position sensor is made on the flywheel.
The power unit (view from the right in the direction of the vehicle):
1 – a belt of a drive of auxiliary units;
2 – a pulley of a drive of auxiliary units;
3 - guide tube of the oil level indicator;
4 – a basic arm of the inlet pipeline;
5 - the lower cover of the timing belt drive;
6 - inlet pipeline;
7 - throttle assembly;
8 – the top cover of a belt of a drive of the gas-distributing mechanism;
9 - oil filler cap;
10 - ignition coil;
11 – a pulley of the pump of the hydraulic booster of a steering;
12 - generator;
13 - belt support roller;
14 - belt tensioner roller;
15 - air conditioning compressor pulley;
16 - oil pan
Connecting rods - steel, I-section, processed together with covers. The covers are attached to the connecting rods with special bolts and nuts.
Piston pin - steel, tubular section. The pin, pressed into the upper head of the connecting rod, rotates freely in the piston bosses.
The piston is made of aluminum alloy. The piston skirt has a complex shape: in the longitudinal section it is barrel-shaped, in the transverse section it is oval. Three grooves for piston rings are machined in the upper part of the piston. The two upper piston rings are compression rings, and the lower one is oil scraper. Compression rings prevent the breakthrough of gases from the cylinder into the crankcase and contribute to the removal of heat from the piston to the cylinder.
The oil scraper ring removes excess oil from the cylinder walls as the piston moves.
Power unit (view from the left in the direction of the vehicle):
1 - gearbox;
2 - air conditioner compressor;
3 - generator;
4 - thermostat housing;
5 - coolant temperature sensor;
6 – cylinder head;
7 – a cover of a head of the block of cylinders;
8 - ignition coil;
9 - oil filler neck;
10 - fuel rail;
11 - throttle position sensor;
12 - throttle assembly;
13 - inlet pipeline;
14 - intake air temperature sensor;
15 - absolute air pressure sensor in the intake manifold;
16 - cylinder block;
17 - crankshaft position sensor;
18 - vehicle speed sensor
Cylinder head (head cover removed):
1 – the screw of fastening of a head of the block of cylinders;
2 – a support of a camshaft;
3 - valve spring;
4 - spring plate;
5 - crackers;
6 - locknut;
7 - adjusting screw;
8 - bracket;
9 - camshaft pulley;
10 - valve rocker;
11 – a bolt of fastening of an axis of yokes of valves;
12 - the axis of the rocker arms of the valves;
13 - thrust flange of the camshaft
The cylinder head is made of aluminum alloy, common to all four cylinders. It is centered on the block with two bushings and fastened with ten screws. A non-shrink metal gasket is installed between the block and the head. At the top of the cylinder head are five bearings (bearings) of the camshaft. The supports are made one-piece, and the camshaft is inserted into them from the timing drive side. The camshaft is driven by a toothed belt from the crankshaft.
In the extreme bearing neck of the camshaft (from the flywheel side), a groove is made, which includes a thrust flange that prevents axial movement of the shaft. The thrust flange is attached to the cylinder head of the camshaft with five bolts attached to the axis of the rocker arms. The rocker arms are kept from displacement along the axis by two brackets, which are fastened with bolts for attaching the rocker arm axis. Screws are screwed into the rocker arms, which serve to adjust the thermal gaps in the valve drive. The adjusting screws are secured against loosening by locknuts. Seats and valve guides are pressed into the cylinder head.
Valve guides are fitted with oil caps on top of the valve guides. Valves are steel, arranged in two rows, obliquely to the plane passing through the axis of the cylinders. In front (along the direction of the car) there is a row of exhaust valves, and at the back - a row of intake valves. The intake valve plate is larger than the exhaust valve.
The valve is opened by a rocker arm, one end of which rests on the camshaft cam, and the other, through an adjusting screw, on the end of the valve stem. The valve closes under the action of a spring. Its lower end rests on a washer, and its upper end rests on a plate, which is held by two crackers. The folded crackers have the shape of a truncated cone on the outside, and on the inside they are equipped with thrust collars that enter the groove on the valve stem.
Oil pump drive (sump removed):
1 - auxiliary drive pulley;
2 – a forward cover of the block of cylinders;
3 - drive sprocket of the pump drive;
4 - drive chain;
5 - oil pump;
6 - crankshaft;
7 - cylinder block
Engine lubrication - combined. Under pressure, the crankshaft main and connecting rod bearings and camshaft bearings are lubricated. Other engine components are splash lubricated. The pressure in the lubrication system is created by a gear oil pump located in the front in the oil pan and attached to the cylinder block. The oil pump is driven by a chain drive from the crankshaft.
Oil pump:
1 - driven sprocket of the drive;
2 - pump housing;
3 - cover of the pump housing with an oil receiver
The driving sprocket of the pump drive is installed on the crankshaft under the front cover of the cylinder block. A cylindrical belt is made on the sprocket, along which the crankshaft front oil seal works. The sprocket is mounted on the crankshaft without tension and is not fixed with a key. When assembling the engine, the drive sprocket of the pump drive is clamped between the timing gear pulley and the shoulder of the crankshaft as a result of tightening the package of parts with the accessory drive pulley mounting bolt. The torque from the crankshaft is transmitted to the sprocket only due to the frictional forces between the end surfaces of the sprocket, the toothed pulley and the crankshaft.
Warning: If the accessory drive pulley bolt is loosened, the oil pump drive sprocket may begin to rotate on the crankshaft and the engine oil pressure will drop.
The oil receiver is made in one piece with the cover of the oil pump housing. The cover is fastened with five screws to the pump body.
The pressure reducing valve is located in the cover of the pump housing and is kept from falling out by a spring retainer.
The oil from the pump passes through the oil filter and enters the oil line made in the cylinder block. Oil filter - full-flow, non-separable. From the line, oil flows to the main bearings of the crankshaft and further, through the channels in the crankshaft, to the connecting rod bearings. Through a vertical channel in the cylinder block, oil from the line is supplied to the cylinder head - to the middle bearing of the camshaft. An annular groove is made in the middle support neck of the camshaft, through which the oil passes to the hollow bolt of the rocker arm axle. Further, the oil, through a hollow bolt, enters the channel made in the axis of the rocker arms, and from there - to the rocker arms and through other hollow axle bolts - to the rest of the camshaft bearings.
Holes are made in the rocker arms through which oil is sprayed onto the camshaft cams.
From the cylinder head, oil flows through vertical channels into the engine sump.
The crankcase ventilation system is closed, forced, with the selection of gases through the oil separator (in the cylinder head cover), which cleans the crankcase gases from oil particles. Gases from the lower part of the crankcase enter through the internal channels in the cylinder head into the head cover and then, through two hoses (the main circuit and the idle circuit), enter the engine intake manifold. Through the main circuit hose, crankcase gases are discharged at partial and full load modes into the space in front of the throttle valve.
Through the idle circuit hose, crankcase gases are discharged into the space behind the throttle valve both in partial and full load modes, and in idling mode.
Control, power, cooling and exhaust systems are described in the relevant chapters.
Source: http://wiki.zr.ru/86-3_%D0%A0%D0%B5%D0%BC%D0%BE%D0%BD%D1%82_Stepway
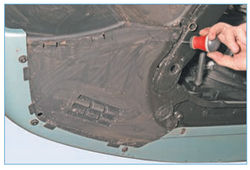
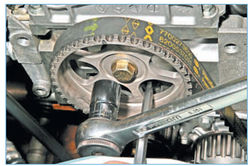
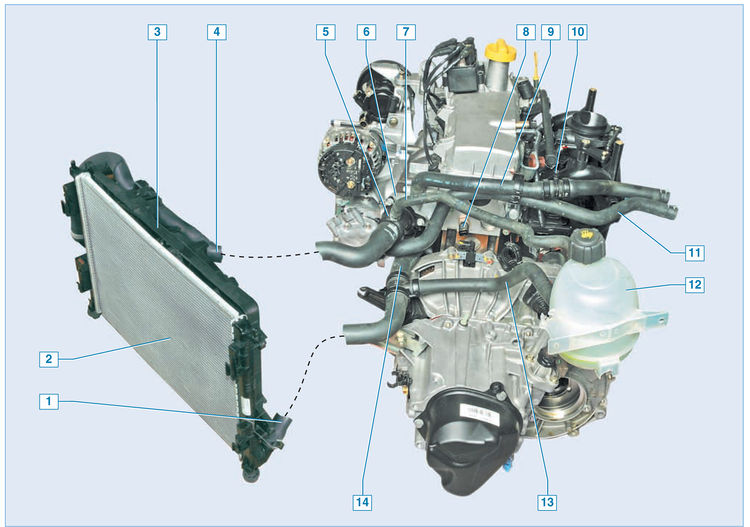
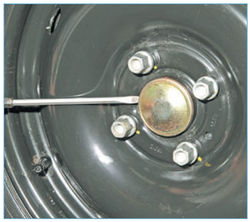

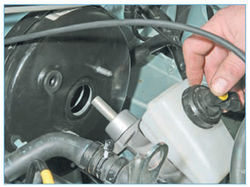

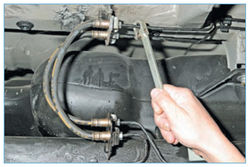
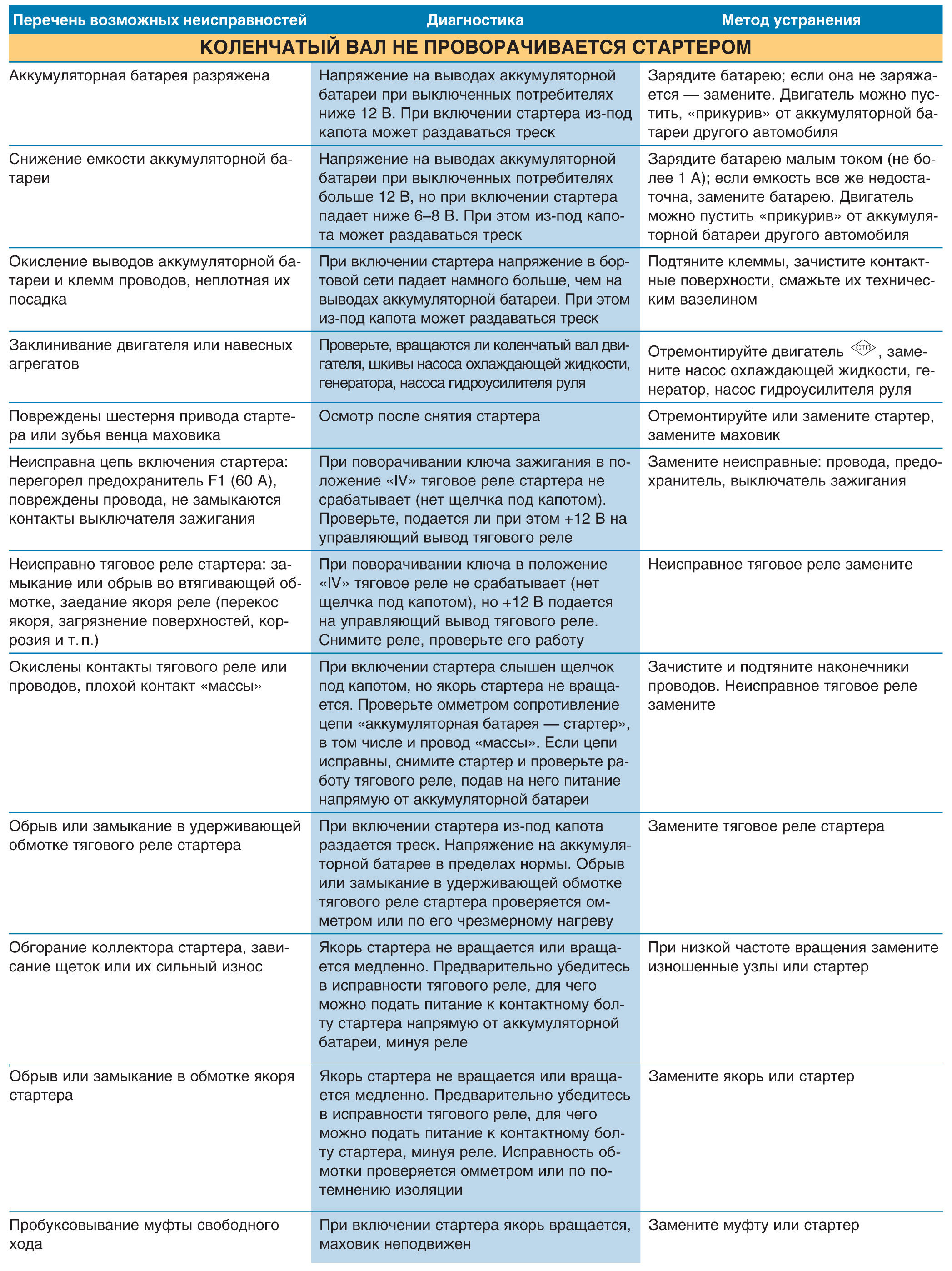
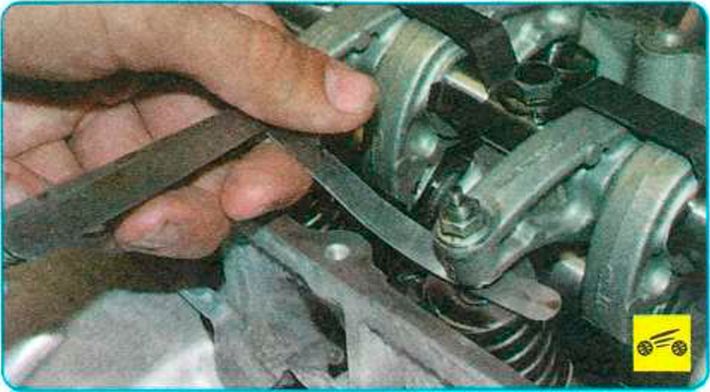