The Ford Focus II is equipped with two independent braking systems: working and parking. The first, equipped with a hydraulic drive, provides braking when the car is moving, the second slows down the car in the parking lot. The working system is double-circuit, with a diagonal connection of the brake mechanisms of the front and rear wheels. One hydraulic drive circuit ensures the operation of the right front and left rear brake mechanisms, the other - the left front and right rear.
If one of the circuits of the working brake system fails, the second circuit is used, which ensures that the car stops with sufficient efficiency.
A vacuum booster is included in the hydraulic drive. By order, an anti-lock braking system (ABS) can be installed on the car, and if it is available, an anti-slip system (TSC) and an exchange rate stability system (ESP) can be installed.
On cars not equipped with ABS, to prevent skidding during heavy braking, pressure regulators are installed in the hydraulic drives of the brake mechanisms of the rear wheels, mounted on the master brake cylinder. In the absence of ABS, a brake force regulator is installed on the rear suspension beam of station wagons, which changes the fluid pressure in the brake mechanisms of the rear wheels depending on the load on the rear axle of the car.
Parking brake system with cable drive on the brake mechanisms of the rear wheels.
Front wheel brake disk, with automatic adjustment of the gap between the pads 2 (Fig. 1) and disk 1, with a floating bracket. The movable bracket is formed by a caliper 3 with a single-piston working cylinder. The shoe guide 4 is bolted to the steering knuckle. The movable bracket is attached with guide pins 5 screwed into the threaded holes of the guide shoe. The guide pins are grease lubricated and protected by plastic bushings. A piston with a sealing ring is installed in the cavity of the working cylinder. Due to the elasticity of this ring, the optimal clearance between the pads and the ventilated disc is maintained. When braking, the piston, under fluid pressure, presses the inner pad against the disc, under the influence of the reaction force, the caliper moves on the fingers and the outer pad is also pressed against the disc, while the pressing force of the pads is the same. When releasing the piston, due to the elasticity of the sealing ring, it is retracted from the pad, as a result, a small gap forms between the pads and the disc.
Fig.1. The brake mechanism of a forward wheel: 1 - a brake disk; 2 - brake pads (the outer one is not visible, as it is closed by a caliper); 3 - brake caliper; 4 - guide pads; 5 - caliper guide pin (located inside the protective sleeve); 6 - air release valve; 7 - brake hose.
Rice. 2. The main brake cylinder: 1 - a reservoir of the main brake cylinder; 2 - tank cap; 3 - brake fluid level sensor; 4 - the main brake cylinder.
Fig.3. vacuum booster
The tandem hydraulic brake master cylinder (Fig. 2) consists of two separate chambers connected to independent hydraulic circuits. The first chamber is connected to the right front and left rear brake mechanisms, the second - to the left front and right rear.
A tank is installed on the main cylinder through rubber connecting bushings, the internal cavity of which is divided by partitions into three compartments. Each compartment feeds one of the brake master cylinder chambers and the clutch release master cylinder.
When you press the brake pedal, the pistons of the main brake cylinder begin to move, the working edges of the cuffs cover the compensation holes, the chambers and the reservoir are separated and the brake fluid is forced out.
A brake fluid level sensor is installed in the upper half of the tank body. If the fluid level falls below the permissible level, the warning lamp for a malfunctioning brake system lights up in the instrument cluster.
Rice. 4. Rear wheel brake mechanism: 1 - rear brake shoe; 2 - tip of the parking brake cable; 3 - shield of the brake mechanism; 4 - clamping brackets of brake pads; 5 - support posts; 6 - expanding lever of the parking brake drive; 7 - spacer bar; 8 - upper coupling spring; 9 - working cylinder; 10 - clearance regulator; 11 - parking brake cable; 12 - front brake shoe; 13 - lower coupling spring.
The vacuum booster (Fig. 3), installed between the pedal mechanism and the main brake cylinder, during braking due to rarefaction in the engine intake pipe through the rod and piston of the first chamber of the main cylinder creates an additional force proportional to the force from the pedal.
A non-return valve is installed in the hose connecting the vacuum booster to the intake manifold. It holds the vacuum in the booster when it drops in the intake manifold and prevents the air-fuel mixture from entering the vacuum booster.
The brake mechanism of the rear wheels is drum, with automatic adjustment of the gap between the shoes and the drum. Brake pads 1 and 12 (fig. 4) are actuated by one hydraulic working cylinder 9 with two pistons. The optimal clearance between the drum and the pads is maintained by a mechanical regulator 10 mounted on the spacer bar 7. Some cars are equipped with rear wheel disc brakes, similar in design to the front wheel mechanisms, but smaller.
The mechanically actuated parking brake consists of a lever mounted on the base of the body between the front seats, a front cable with an adjusting device and an equalizer, to which two rear cables are attached, and expansion levers 6 (see Fig. 4) installed in drum rear wheel brakes. When moving, the expanding levers move the front brake shoe through the spacer bar until it stops against the brake drum and then, having received a hard stop, press the rear shoe against the drum, blocking the drum. If the vehicle is equipped with rear wheel disc brakes, they have swing arms mounted in the caliper. When the lever is turned, the piston of the brake cylinder moves and the pads clamp the disc.
The parking brake does not require special care. During current repairs, check the degree of wear of the teeth of the sector and pawls. Replace excessively worn parts.
The sheaths or wires of the cables, if they are broken, must be replaced with new ones.
The anti-lock braking system (ABS) consists of wheel speed sensors, a brake light switch, a hydraulic unit, a hydro-electronic control unit and a signal lamp. In addition, the anti-lock braking system is equipped with a self-diagnosis system that detects malfunctions of its components.
ABS is used to regulate the pressure in the brake mechanisms of all wheels when braking in difficult road conditions, which prevents the wheels from locking.
The ABS system provides the following benefits:
- detour of obstacles with a higher degree of safety, including during emergency braking;
- reduction of the braking distance during emergency braking while maintaining roadholding and controllability of the car, including when turning.
In the event of a system failure, functions for diagnosing and maintaining operation in case of system failures are provided.
The hydroelectronic control unit (GEBU), shown in fig. 5 receives information about vehicle speed, direction of travel and road conditions from the wheel speed sensors. After the ignition is turned on, the ABS module supplies voltage to the sensors. The sensors use the Hall effect, they generate an output signal in the form of rectangular pulses. The signal changes in proportion to the rotational speed of the encoder pulse ring built into the front hub bearing seal and directly into the rear hub.
Based on this information, the GEBU determines the optimal wheel braking mode.
There are the following modes of operation of the anti-lock braking system:
- normal braking mode. During normal braking, the solenoid valve is de-energized, the inlet valve is open, the outlet valve is closed. When the brake pedal is pressed, pressurized brake fluid is supplied to the working cylinder through the solenoid valve and actuates the wheel brakes. When the brake pedal is released, the brake fluid returns to the brake master cylinder through the inlet and check valves;
- emergency braking mode. If during emergency braking the wheel locks up, the GEBU issues a command to the solenoid valve to reduce the supply of brake fluid, then voltage is applied to each solenoid valve. The inlet valve closes and the brake fluid supply from the master cylinder is shut off; the outlet valve opens, and the brake fluid flows from the working cylinder to the master cylinder, and then to the reservoir, which causes a decrease in pressure;
- pressure maintenance mode. With a maximum decrease in pressure in the working cylinder, the GEBU issues a command to the solenoid valve to maintain brake fluid pressure, voltage is applied to the inlet valve and is not applied to the outlet valve. At the same time, the inlet and outlet valves are closed and the brake fluid does not leave the working cylinder;
- pressure increase mode. If the GEBU determines that the wheel is not blocked, then it de-energizes the solenoid valve. Voltage is not applied to the solenoid valves, the brake fluid through the inlet valve enters the working cylinder, the pressure in which increases.
Diagnostics and repair of the anti-lock braking system requires special equipment and accessories. Therefore, in case of failure, contact a specialized service station.
The hydraulic brake system is integrated into a single unit with metal tubes and hoses. The system is filled with a special brake fluid of at least DOT-4 class, which must be replaced periodically.
Rice. 5. Hydroelectronic control unit
Useful advice
Some drivers, in an effort to wear out the parking brake cables less, try to use them less often.
Such "economy" leads to the opposite result: the cable, rarely moving in the shell, gradually loses its mobility, it jams, as a result, the cable breaks. Therefore, use the parking brake whenever necessary. The free travel of the brake pedal with the engine off should be approximately 3-8 mm. Too little free play indicates an incorrect initial setting of the brake pedal or seizure of the working cylinder, causes increased fuel consumption and accelerated wear of the brake pads. Too much free play is a sign of excessive clearances in the pedal mechanism or a violation of the tightness of the hydraulic brake system. If the free play decreases when the pedal is pressed repeatedly, i.e. it becomes "harder", there is air in the system. If the full pedal travel starts to increase, the system is leaking.
If the brake pedal always starts to vibrate when braking, most likely the brake discs are warped. Unfortunately, in such a situation, they only need to be changed, and both at once. Periodically appearing and disappearing pedal vibration during sudden braking of a car equipped with an anti-lock braking system accompanies the operation of this system and is not a sign of a malfunction.
If the car starts to pull to the side when braking, check the working cylinders: they may need to be replaced.
If there is a knock in the front suspension that disappears when braking, check the tightness of the caliper mounting bolts.
After replacing the brake pads, before driving, be sure to press the brake pedal several times - the pistons in the working cylinders should fall into place.
Source: http://www.samoremont-avto.ru/ford-focus2-repair-manual-p198.html.
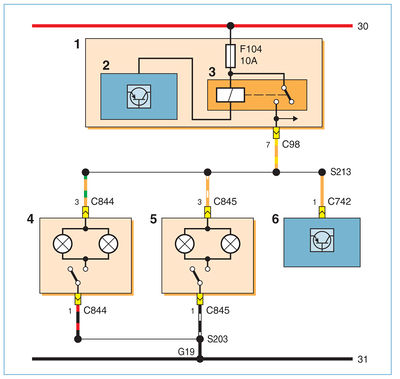
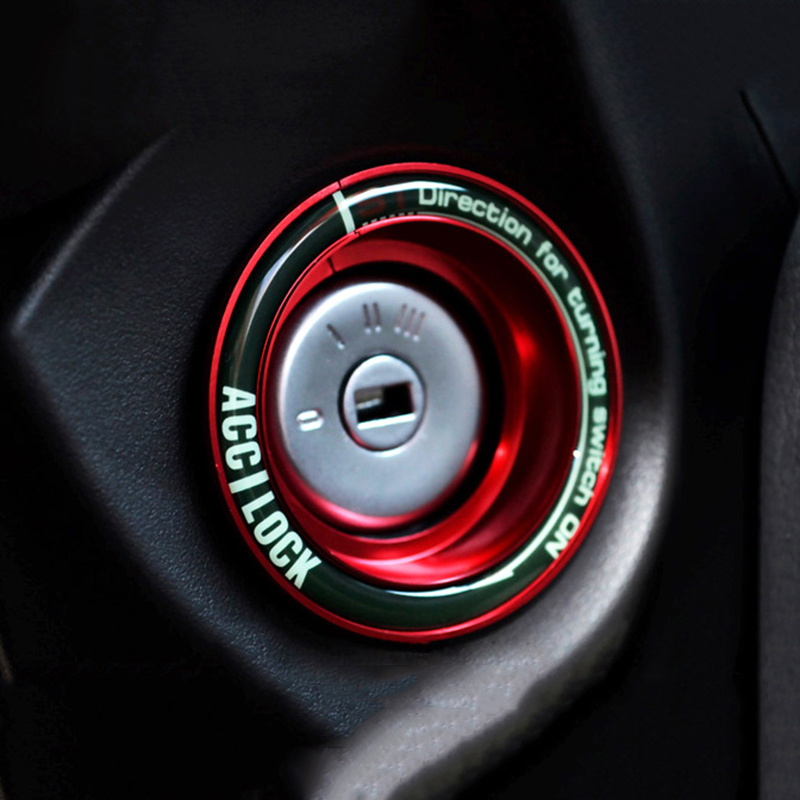

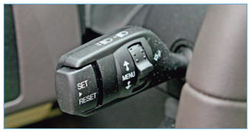
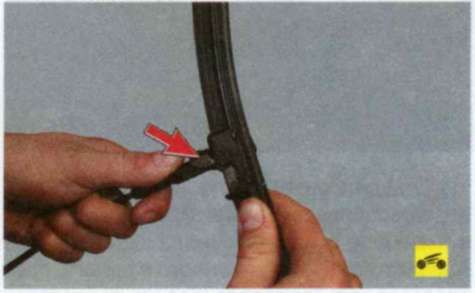
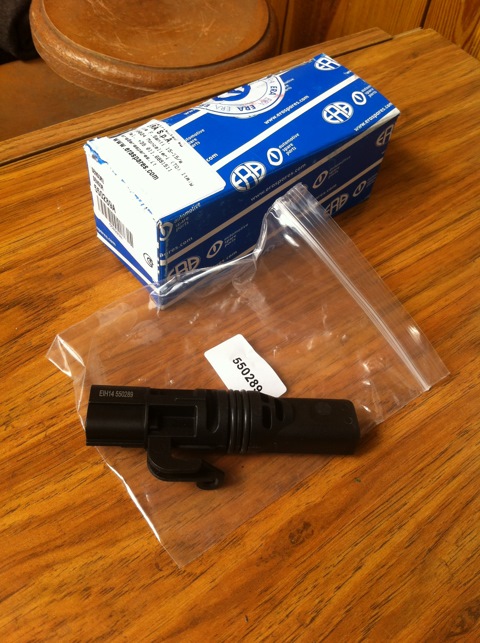
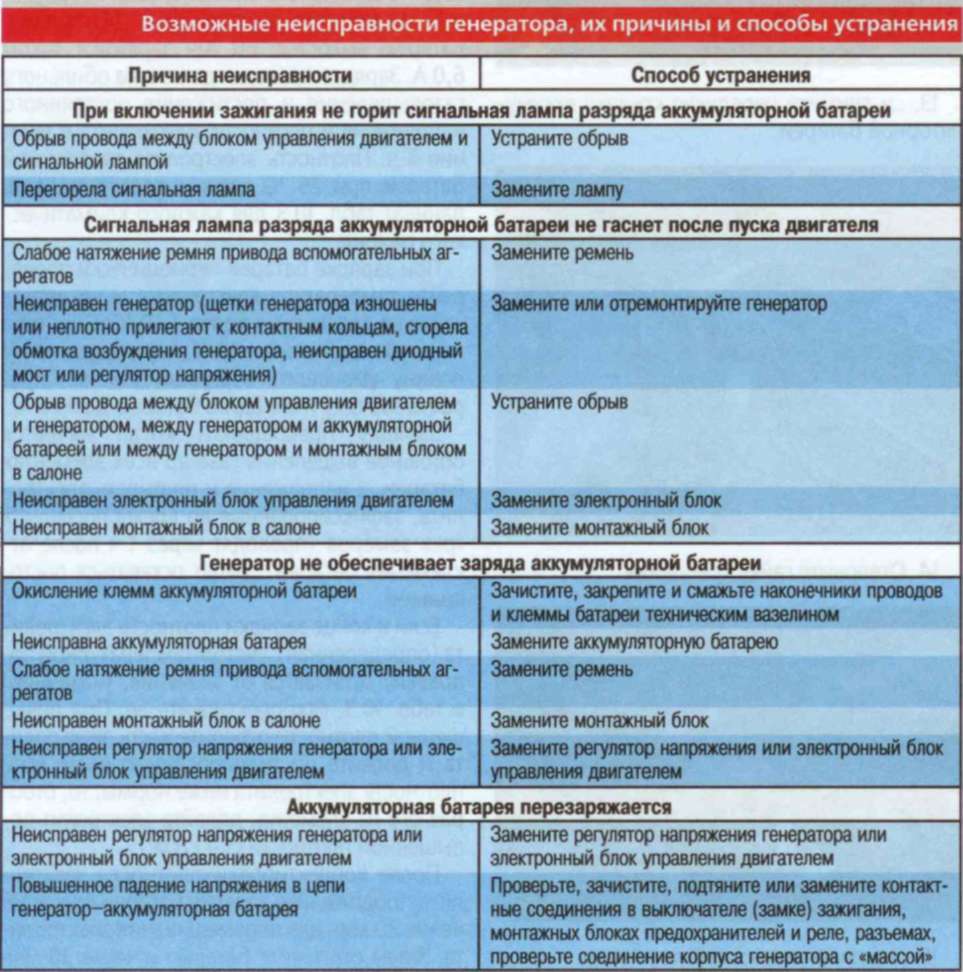