Инструменты:
- Щуп плоский
- Линейка
- Штангенциркуль
- Нутромер
- Микрометр
- Шабер механический
- Напильник плоский
- Калибровочная проволока
Детали и расходники:
- Поршень с кольцами (при необходимости замены)
- Блок цилиндров в сборе с крышками коренных подшипников (при необходимости замены)
- Поршневые пальцы (при необходимости замены)
- Шатун (при необходимости замены)
- Расширитель маслосъемного кольца (при необходимости замены)
- Коленчатый вал (при необходимости замены)
- Полукольца коленчатого вала (при необходимости замены)
- Шатунные вкладыши (при необходимости замены)
- Коренные вкладыши (при необходимости замены)
1. Очистите головку поршня от нагара. Если на поршне обнаружены задиры, следы прогара, глубокие царапины или трещины, замените поршень. Прочистите канавки под поршневые кольца. Это удобно делать обломком старого кольца.
2. Проверьте щупом зазоры между кольцами и канавками на поршне.
Таблица предельно допустимых значений зазоров поршневых колец.
3. Наиболее точно зазоры можно определить замером колец и канавок на поршне. Для этого измерьте микрометром толщину колец в нескольких местах по окружности, а затем с помощью набора щупов измерьте ширину канавок в нескольких местах по окружности. Вычислите среднеарифметические значения зазоров (разница между толщиной кольца и шириной канавки). Если хотя бы один из зазоров больше предельно допустимого значения, замените поршень с кольцами.
4. Измерьте зазоры в замках колец, вставив кольцо в специальную оправку. При отсутствии оправки вставьте кольцо в цилиндр, в котором оно работало (или будет работать, если кольцо новое), продвиньте поршнем как оправкой кольцо в цилиндр на 15—20 мм, чтобы оно установилось в цилиндре ровно, без перекосов, и измерьте щупом зазор в замке кольца. Если зазор больше предельно допустимого значения, замените кольцо.
5. Если зазор меньше номинального, аккуратно сточите напильником торцы кольца.
6. Тщательно очистите поверхности блока цилиндров от остатков старых уплотнительных прокладок. Внимательно осмотрите блок. Если обнаружите трещины, замените блок в сборе с крышками коренных подшипников.
7. Осмотрите цилиндры. Если на зеркале цилиндров появились царапины, задиры или другие дефекты, расточите цилиндры под ремонтный размер (эту работу рекомендуется выполнять в специализированной мастерской) или замените блок цилиндров. При различных дефектах глубиной более 0,2 мм блок ремонту не подлежит и его надо заменить.
Примечание:
При осмотре цилиндров рекомендуется освещать зеркала цилиндров переносной лампой - так дефекты видны значительно лучше.
8. Определите нутромером фактические диаметры цилиндров. Диаметр цилиндра измеряйте в трех поясах. В каждом поясе диаметр измеряют в двух взаимно перпендикулярных направлениях (в продольном и поперечном). В зоне над поясом А цилиндры практически не изнашиваются. По разнице размеров в этой зоне и в остальных поясах можно судить об износе цилиндров. Номинальный диаметр цилиндра 87.600 мм, овальность и конусность не должны быть более 0.015 мм. Если максимальный диаметр больше 87.600 мм или овальность превышает указанное значение, расточите цилиндры до ремонтного размера поршней, оставив припуск на диаметр под хонингование. Затем отхонингуйте цилиндры, выдерживая такой диаметр Б, чтобы при установке выбранного ремонтного поршня расчетный зазор между ним и цилиндром был 0.05 мм. Дефектовку, расточку и хонингование блока проводите в мастерских, располагающих специальным оборудованием.
Схема измерения цилиндров
А - пояс наибольшего износа (на расстоянии 12 мм от поверхности разъема с головкой блока);
Б - зона измерения после растачивания и хонингования (на расстоянии 64 мм от поверхности разъема с головкой блока);
В - пояс наименьшего износа (на расстоянии 115 мм от поверхности разъема с головкой блока).
9. Проверьте отклонение от плоскостности поверхности разъема блока с головкой блока цилиндров. Приложите штангенциркуль (или линейку) к плоскости:
- в середине блока;
- в продольном и поперечном направлениях;
- по диагоналям поверхности.
В каждом положении определите плоским щупом зазор между линейкой и плоскостью. Это и есть отклонение от плоскостности. Номинальное отклонение 0.05 мм. Если отклонение больше 0.1 мм, замените блок.
10. Проверьте зазоры между поршнями и цилиндрами. Зазор определяется как разность между измеренными диаметрами поршня на расстоянии 12 мм от нижнего края юбки по оси, перпендикулярной поршневому пальцу, и цилиндра в зоне В. Если зазор больше 0.050 мм, расточите цилиндры и установите поршни ремонтного размера. На двигатель должны быть установлены поршни одного размера.
11. Осмотрите поршневые пальцы. Пальцы с трещинами замените.
12. Вставьте палец в шатун. Если при покачивании пальца ощущается люфт, замените палец или шатун.
13. Замените сломанные кольца и расширитель маслосъемного кольца.
14. Замените погнутые шатуны.
15. Если на поверхностях коленчатого вала, по которым работают сальники, появились глубокие риски, царапины, забоины, вал необходимо заменить.
16. Замените полукольца, если на их рабочих поверхностях обнаружены задиры, риски и отслоения. На полукольцах запрещается проводить любые подгоночные работы.
Новые и изношенные полукольца коленчатого вала
Примечание:
После установки вкладышей в постели их концы немного выступают наружу, поэтому для правильной ориентации вкладышей при окончательной затяжке болтов крепления крышек подшипников проследите за тем, чтобы выступание обоих концов было одинаковым. Обратите внимание на канавки полуколец: этими сторонами полукольца должны быть установлены к щекам коленчатого вала.
17. Измерьте осевой зазор коленчатого вала. Увеличенный зазор указывает на износ опорных фланцев коленчатого вала. В этом случае замените коленчатый вал. Если это не приведет к уменьшению осевого зазора, придется заменить блок цилиндров.
18. Осмотрите шатунные и коренные вкладыши. Замените вкладыши с задирами и выкрашиванием рабочего слоя. На вкладышах запрещается проводить любые подгоночные работы.
19. Проверьте зазоры между вкладышами коренных и шатунных подшипников и соответствующими шейками коленчатого вала. Эту работу рекомендуется выполнять в специализированной мастерской.
Измерение радиального зазора
Принцип измерения зазора заключается в сплющивании специальной пластиковой калибровочной проволоки и измерении ширины полученного отпечатка.
Для измерения зазора между коренной шейкой и вкладышами используется отрезок калибровочной проволоки, длина которого на 2 мм короче, чем ширина вкладыша.
Калибр расположите в осевом направлении на шейке вала.
Накройте крышкой с утановленным вкладышем. Чтобы калибр не сдвинулся в момент установки крышки, его можно "приклеить" к шейке вала тонким слоем консистентной смазки.
Не проворачивайте коленвал! Открутите болты и снимите крышку с вкладышем.
Используя специальный измерительный шаблон, измерьте ширину отпечатка расплющенной калибровочной проволоки. Отпечаток может остаться на шейке вала.
Либо на вкладыше.
По специальной таблице пересчета, нанесенной на шаблон, определите зазор в соединении.
В статье не хватает:
- Фото инструментов
- Качественных фото ремонта
Источник: http://carpedia.club
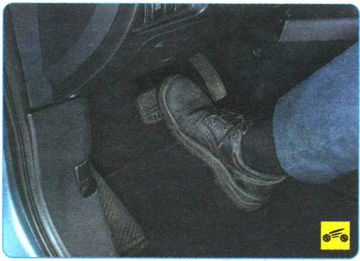
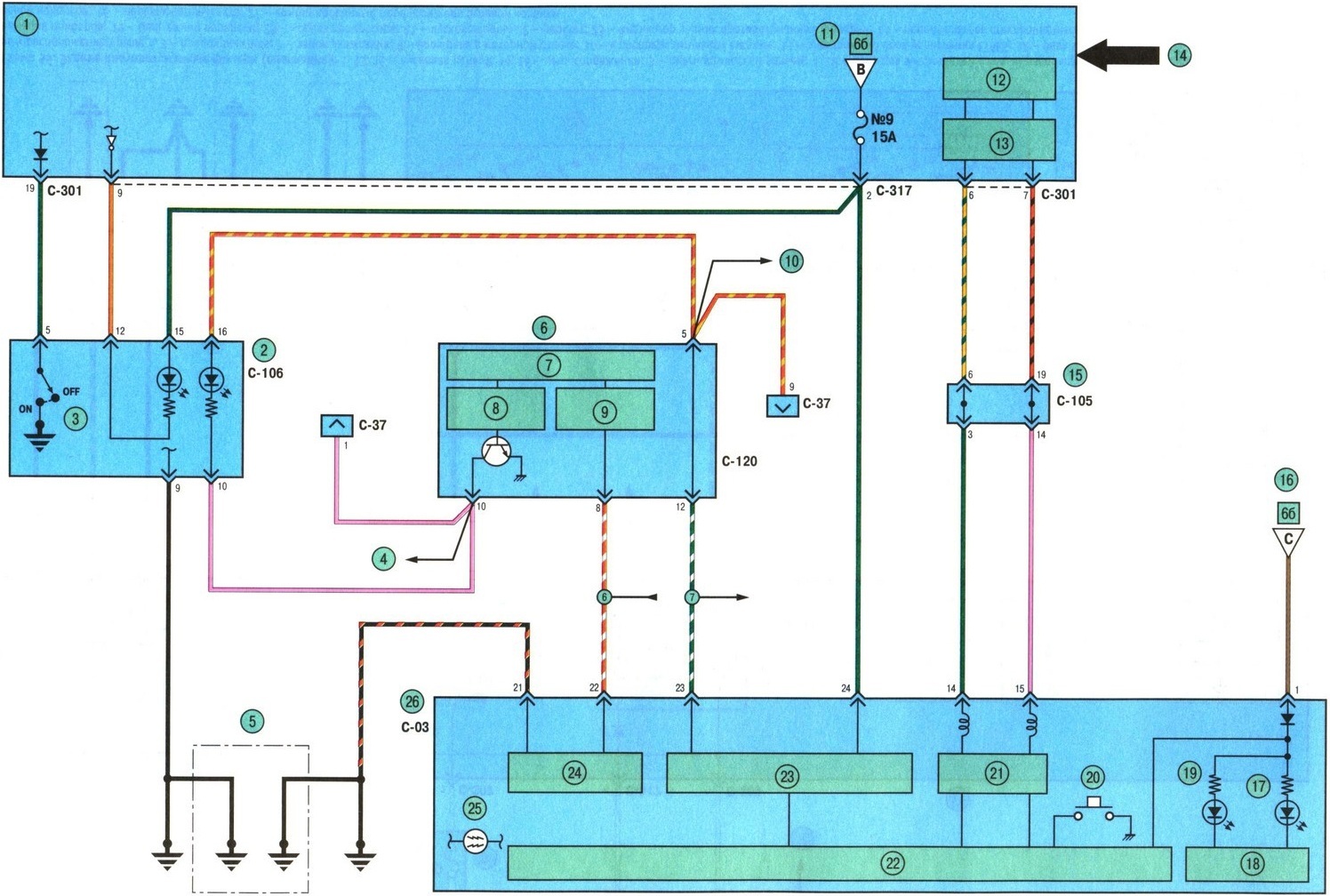
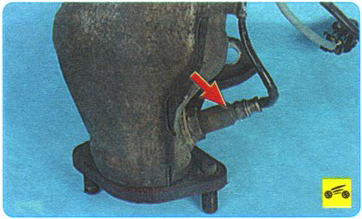
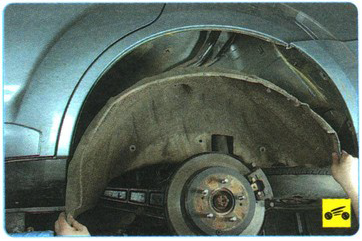
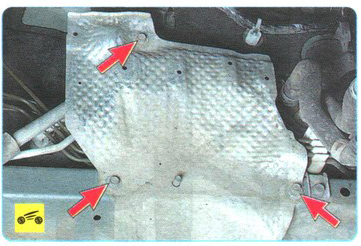
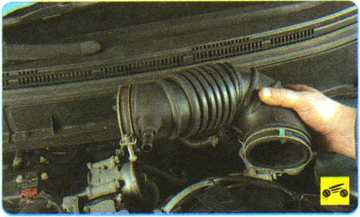
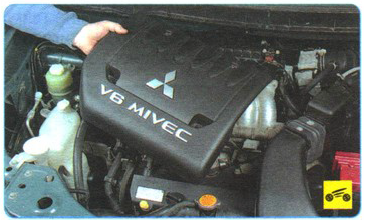
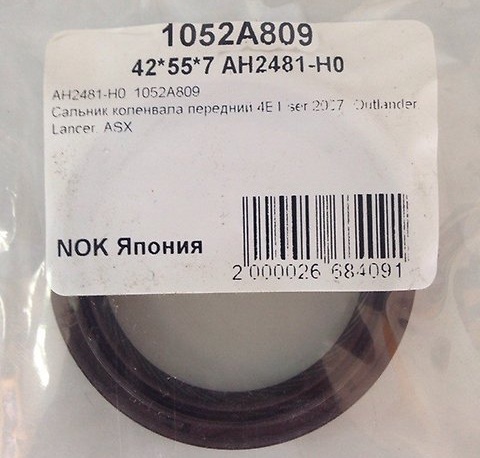