Инструменты:
- Нож (или скребок)
- Шабер
- Поверочная линейка
- Щуп плоский
- Компрессор
- Пневмопистолет для обдувки
- Нутромер
- Микрометр
- Измерительная головка часового типа с штативом
- Стенд для измерения осевого биения
- Ключ трещоточный
- Головка на 16 мм
- Динамометрический ключ
- Приспособление для измерения скручивания и изгиба шатуна
- Специальный инструмент с угловым индикатором МВ991614
- Кисть флейцевая
Детали и расходники:
- Коленчатый вал 0501.L8 (при необходимости)
- Упорное полукольцо 0118.G0 - 2 шт. (при необходимости)
- Верхний вкладыш коренного подшипника коленчатого вала 0113.Y3 - 5 шт. (при необходимости)
- Нижний вкладыш коренного подшипника коленчатого вала 0113.X9 - 5 шт. (при необходимости)
- Вкладыш шатунного подшипника коленчатого вала 0606.Y6 - 8 шт. (при необходимости)
- Маховик двигателя 0532.S2 (при необходимости)
- Пластина привода гидротрансформатора 0535.A9 (при необходимости)
- Переходная пластина 0535.A7 (при необходимости)
- Задний сальник коленчатого вала 0127.51 (при необходимости)
- Блок цилиндров двигателя 1050A750 (при необходимости)
- Шатун в сборе 0603.A5 - 4 шт. (при необходимости)
- Поршень с поршневым пальцем 0627.63/0627.64/0627.65/0627.62 - 4 шт. (при необходимости)
- Комплект поршневых колец 0627.66/0627.67 - 4 шт.
- Пластиковый калибр Plastigauge PL-А (0,025 - 0,175 мм)
- Очиститель (или растворитель)
- Обезжириватель
- Проникающий краситель
- Моторное масло
- Краска
- Ветошь
Примечания:
Как снять двигатель Пежо 4007 и провести его разборку, а также какие инструменты при этом используются, смотрите здесь и здесь.
Шатунно поршневая группа двигателя вместе с коленчатым валом являются основным рабочим механизмом ДВС. Поэтому поддержание исправности рабочего механизма обеспечивает продолжительный срок службы двигателя с оптимальными показателями его технической эксплуатации.
При диагностике блока цилиндров, коленчатого вала и деталей поршневой группы необходимо проводить такие работы, как: проверка зазора в коренных подшипниках коленчатого вала, некруглости и конусности коренных и шатунных шеек коленчатого вала, биение маховика, проверка износа цилиндра, зазора между поршнем и цилиндром.
Проверка блока цилиндров
1. Перед очисткой блока цилиндров проверьте отсутствие следов течей охлаждающей жидкости или каких-либо очевидных повреждений.
Примечание:
При выявлении повреждений, которые нельзя отремонтировать без потери свойств материалов, рекомендуется заменить блок цилиндров.
2. Очистите детали от грязи, масла, углеродных остатков, накипи и других видов отложений, после чего можно приступить к проверке и ремонтным операциям.
3. Удалите осадки с масляных отверстий и убедитесь, что эти отверстия не забиты грязью и отложениями. При необходимости продуйте сжатым воздухом отверстия каналов системы смазки и системы охлаждения.
4. Все детали должны быть аккуратно разложены в соответствии с порядком сборки.
5. Визуально проверьте блок цилиндров на отсутствие остатков прокладки или других посторонних частиц и повреждений. При обнаружении дефектов устраните их или замените блок цилиндров.
6. Проверьте блок цилиндров с помощью жидкого раствора (проникающего красителя) для определения наличия трещин. Если дефекты очевидны, то замените блок цилиндров.
7. С помощью поверочной линейки и плоского щупа проверьте степень коробления рабочих поверхностей блока цилиндров в направлениях, показанных на рисунке. Поверхность блока цилиндров должна быть очищена от посторонних частиц.
Примечание:
Номинальное значение – 0,05 мм или меньше; предельно допустимое значение – 0,1 мм.
8. Если коробление значительно, то исправьте дефект до допустимой величины или замените блок цилиндров.
Примечание:
Предельно допустимая глубина шлифования – 0,20 мм.
Общая толщина снимаемого металла с привалочных поверхностей головки блока цилиндров и блока цилиндров не должна превышать в сумме 0,2 мм.
9. Проверьте зеркало цилиндра на отсутствие царапин и следов заедания (задиров). Если дефекты очевидны, отремонтируйте или замените блок цилиндров.
10. Проверьте износ цилиндров с помощью индикатора-нутромера. Для этого измерьте диаметр цилиндра, а также овальность (отклонение от крутости) и конусность (отклонение от цилиндричности) цилиндра.
Примечание:
Номинальное значение внутреннего диаметра цилиндра двигателя – 88,00 - 88,03 мм.
Предельно допустимая конусность (отклонение от цилиндричности) – 0,15 мм.
Измерения проводите в местах, показанных на рисунке (в трех поясах по высоте).
11. При наличии сильного износа цилиндра либо если конусность или некруглость (овальность) цилиндра больше предельно допустимого значения, то замените блок цилиндров.
Примечание:
После замены блока цилиндров необходимо подобрать соответствующие поршни и поршневые кольца.
12. Измерьте наружный диаметр поршня в месте, показанном на рисунке.
Примечание:
Наружный диаметр поршня – 87,97 - 88,00 мм.
13. По результатам измерения диаметра цилиндра и наружного диаметра поршня, определите зазор между поршнем и цилиндром, который должен находится в указанном диапазоне: 0,02 - 0,04 мм.
14. Если определенный (вычисленный) зазор не соответствует указанному значению, то замените блок цилиндров.
Примечание:
После замены блока цилиндров необходимо подобрать соответствующие поршни и поршневые кольца.
Проверка коленчатого вала
1. Проверьте коренные и шатунные шейки коленчатого вала на отсутствие повреждений (задиры, прихваты), чрезмерного износа (см. первое фото ниже) и трещин (см. второе фото ниже). Кроме того, проверьте отверстия масляных каналов на отсутствие засорения. При необходимости, замените коленчатый вал.
Примечание:
В случае замены коленчатого вала необходимо подобрать новые вкладыши коренных и шатунных подшипников коленчатого вала.
Процедура подбора вкладышей шатунных и коренных подшипников коленчатого вала приведена здесь.
2. Проверьте некруглость и конусность коренных и шатунных шеек, как показано на рисунке.
Примечание:
Предельно допустимые значения: некруглость – не более 0,003 мм; конусность – не более 0,005 мм.
3. Если некруглость или конусность больше предельно допустимого значения, то замените коленчатый вал.
4. Измерьте наружный диаметр коренной шейки коленчатого вала и внутренний диаметр вкладыша коренного подшипника коленчатого вала в двух взаимно перпендикулярных направлениях (на рисунке обозначены "А" и "В") и в двух сечениях по длине (на рисунке обозначены "1" и "2").
Примечание:
Наружный диаметр коренной шейки коленчатого вала – 51,973 - 51,988 мм.
Зазор в коренном подшипнике: номинальный – 0,012 - 0,030 мм; предельно допустимый – 0,08 мм.
Здесь смотрите, как определить величину зазора в коренных подшипниках коленчатого вала методом пластикового калибра.
5. Если величина зазора превосходит предельно допустимое значение, то замените вкладыши коренного подшипника и, если необходимо, коленчатый вал.
Примечание:
Не подвергайте механической обработке подшипник или постель коленчатого вала для регулировки зазора.
Если нельзя получить номинальный зазор, используя подбор вкладышей, то замените коленчатый вал.
Проверка вкладышей коренных подшипников
1. Визуально проверьте состояние поверхности вкладыша коренного подшипника (неравномерный контакт, полосы, царапины, задиры и др.). В случае очевидного наличия дефектов замените вкладыши коренного подшипника.
Примечание:
Если вкладыш нуждается в замене, то выберите и установите вкладыш требуемого размера. Как это сделать, смотрите здесь.
2. Если имеются дефекты (полосы и задиры), то проверьте соответствующие шейки коленчатого вала (см. выше в разделе проверки коленчатого вала).
3. Проверьте зазор в коренном подшипнике, как описано в п.4 выше (раздел проверки коленчатого вала) или здесь.
Проверка заднего сальника коленчатого вала
1. Проверьте рабочую кромку сальника коленчатого вала на отсутствие износа или повреждения.
2. Проверьте резиновую часть сальника на отсутствие затвердевания или разрушения.
Примечание:
При выявлении дефектов замените задний сальник коленчатого вала.
Проверка маховика или пластины привода гидротрансформатора
1. Как проверить маховик (пластину привода гидротрансформатора), смотрите здесь.
Примечание:
При необходимости, замените маховик (пластину привода гидротрансформатора).
Проверка упорных полуколец
1. Проверьте состояние поверхности каждого полукольца (отслаивание, неравномерный контакт, риски, задиры и износ). Замените при необходимости.
2. Установите вкладыши коренных подшипников на блок цилиндров и упорные полукольца. Уложите коленчатый вал на подшипники и проверьте, что осевой зазор коленчатого вала соответствует номинальному значению. Если осевой зазор превышает предельно допустимое значение, то замените упорные полукольца.
Примечание:
Осевой зазор коленчатого вала: номинальное значение – 0,05 - 0,25 мм; предельно допустимое значение – 0,40 мм.
Проверка поршня и поршневого пальца
Примечание:
Поршень и поршневой палец необходимо заменять как комплект.
1. Проверьте поршни на отсутствие царапин, задиров, износа и других дефектов (особенно на упорных поверхностях). Замените поршень при наличии дефектов.
Примечание:
Перед проверкой поршня, удалите отложения нагара с его верхней поверхности.
Если на поршне имеется какие-либо дефекты, то проверьте также зеркало цилиндра (см. раздел проверки блока цилиндров).
При необходимости замены поршня одновременно следует заменить его поршневые кольца.
2. Попытайтесь вставить поршневой палец в отверстие поршня усилием большого пальца. При этом должно чувствоваться сопротивление. Замените палец, если он легко входит в отверстие или имеется значительный люфт.
Проверка поршневых колец
Примечание:
Если поршень заменяется новым, то поршневые кольца также необходимо заменить новыми.
1. Проверьте каждое поршневое кольцо на отсутствие изломов, повреждений или значительного износа. Замените дефектные кольца.
2. Измерьте зазор между поршневым кольцом и канавкой поршня. Если измеренный зазор превышает предельно допустимое значение, то установите новое поршневое кольцо и повторно измерьте зазор. Если измеренный зазор снова превышает предельно допустимое значение, то замените поршень. Если измеренный зазор меньше предельно допустимого значения, то замените только поршневые кольца.
Примечание:
Зазор между компрессионным кольцом и канавкой под него: номинальное значение – 0,03 - 0,07 мм; предельно допустимое значение – 0,10 мм.
Перед выполнением измерений удалите отложения нагара из всех канавок поршня.
Измерение зазора между кольцом и канавкой поршня выполните по всей окружности кольца.
3. Установите поршневое кольцо в отверстие цилиндра. Переместите кольцо поршнем, как показано на рисунке, это позволит кольцу встать под прямым углом к образующей стенки цилиндра. Измерьте зазор в замке кольца с помощью плоского щупа. Если зазор больше предельно допустимого значения, то замените поршневое кольцо.
Примечание:
Номинальное значение зазора в замке поршневого кольца: компрессионное кольцо №1: 0,15 - 0,25 мм; компрессионное кольцо №2 – 0,30 - 0,45 мм; маслосъемное кольцо – 0,10-0,35 мм.
Предельно допустимое значение зазора в замке поршневого кольца: компрессионные кольца №1 и №2 – 0,8 мм; маслосъемное кольцо – 1,0 мм.
4. При замене поршневых колец без замены блока цилиндров (или если не выполнялась механическая обработка цилиндров), проверяйте зазор в замке поршневых колец в точке, расположенной в нижней части цилиндра (зона наименьшего износа).
Проверка вкладышей шатунных подшипников
1. Визуально проверьте состояние поверхности вкладыша шатунного подшипника (неравномерный контакт, полосы, царапины, задиры и др.). В случае очевидного наличия дефектов замените вкладыши шатунного подшипника.
2. Если имеются дефекты (полосы и задиры), то проверьте соответствующие шейки коленчатого вала (см. в разделе проверки коленчатого вала и блока цилиндров выше). Если имеются дефекты на шейках коленчатого вала, то замените коленчатый вал.
Примечание:
В случае замены коленчатого вала необходимо подобрать новые вкладыши коренных и шатунных подшипников коленчатого вала.
Как правильно подобрать вкладыши, смотрите здесь.
3. Измерьте внутренний диаметр шатунного подшипника и наружный диаметр шатунной шейки коленчатого вала, затем определите зазор в шатунном подшипнике.
Примечание:
Для измерения зазора в шатунном подшипнике можно использовать пластиковый калибр.
Наружный диаметр шатунной шейки коленчатого вала – 47,954 - 47,972 мм.
Зазор в шатунном подшипнике: номинальный – 0,018 - 0,045 мм; предельно допустимый – 0,10 мм.
4. Если масляный зазор превышает предельно допустимое значение, то замените, если необходимо, вкладыши шатунного подшипника или коленчатый вал, или обе детали.
Проверка шатуна
1. Установите поршневой палец в шатун, если он был снят.
2. Установите шатун в специальный прибор "С" вместе с установленными верхним и нижним вкладышами шатунного подшипника (см. рисунок ниже, в п.4).
3. Затяните болты крепления крышки шатуна в соответствии со специальной процедурой.
4. Проверьте изгиб "А" и скручивание "В" шатуна, как показано на рисунке.
Примечание:
Предельно допустимое значение (на 100 мм длины): изгиб – 0,05 мм; скручивание – 0,10 мм.
5. Измерьте геометрические параметры шатуна.
Примечание:
Диаметр верхней головки шатуна (d) – 20,974 - 20,985 мм.
Диаметр нижней головки шатуна (D) – 51,000 - 51,018 мм.
Длина шатуна (L) – 143,75 мм. Длина шатуна (L) – расстояние между центрами верхней и нижней головок шатуна.
6. Если изгиб или скручивание шатуна превысили предельно допустимое значение по техническим требованиям, то замените шатун в сборе с крышкой.
В статье не хватает:
- Фото инструмента
- Фото деталей и расходников
Источник: carpedia.club
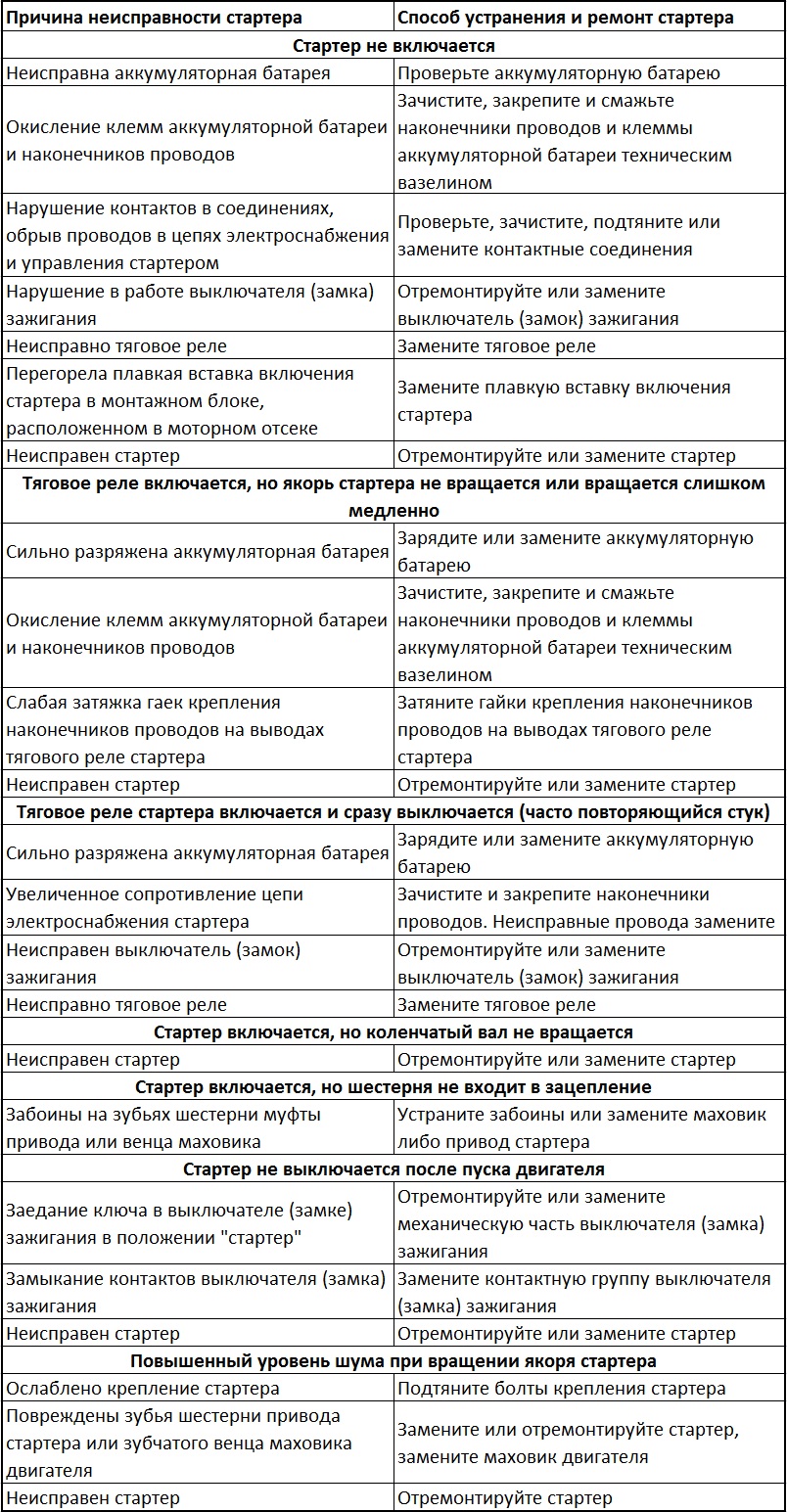
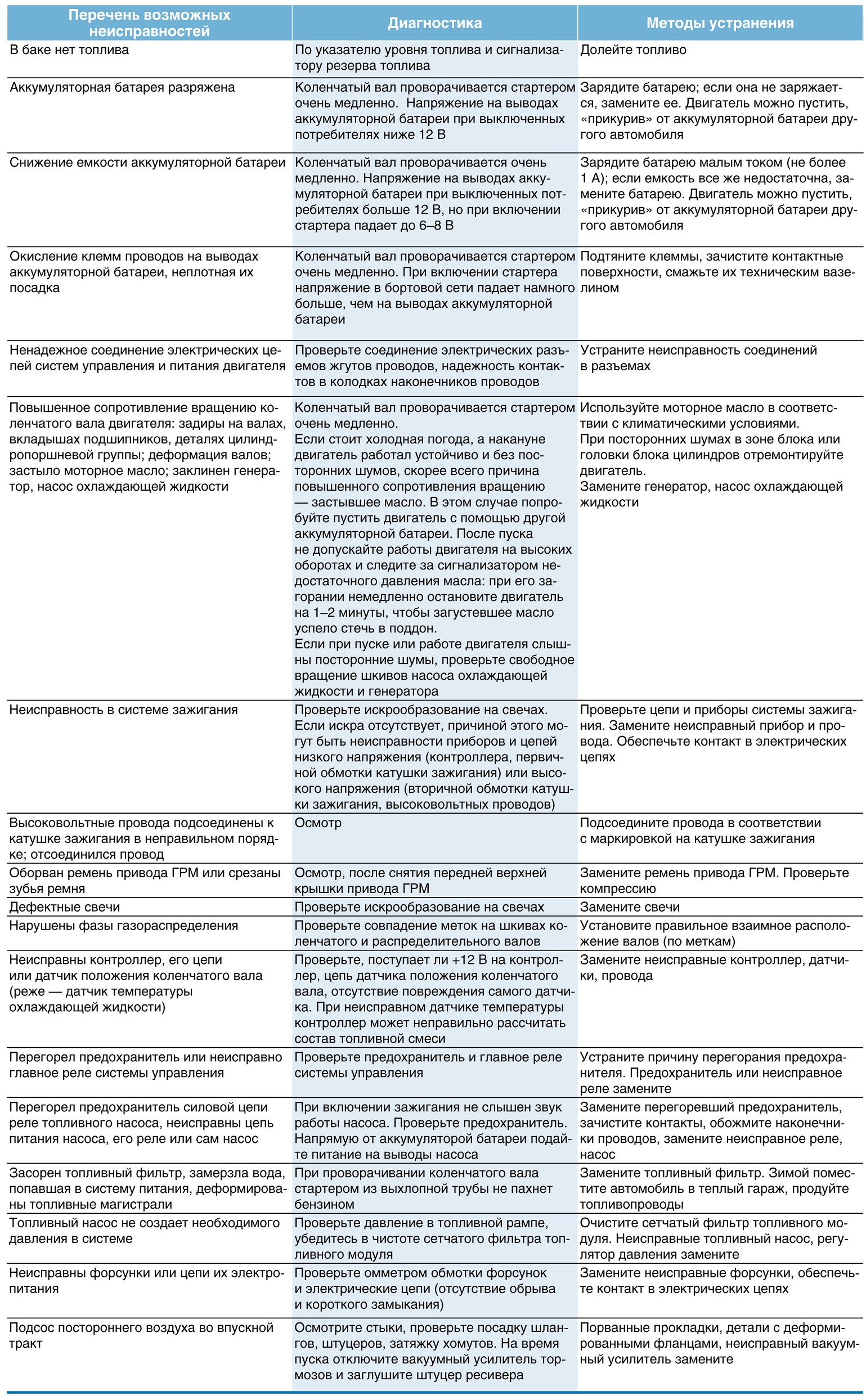
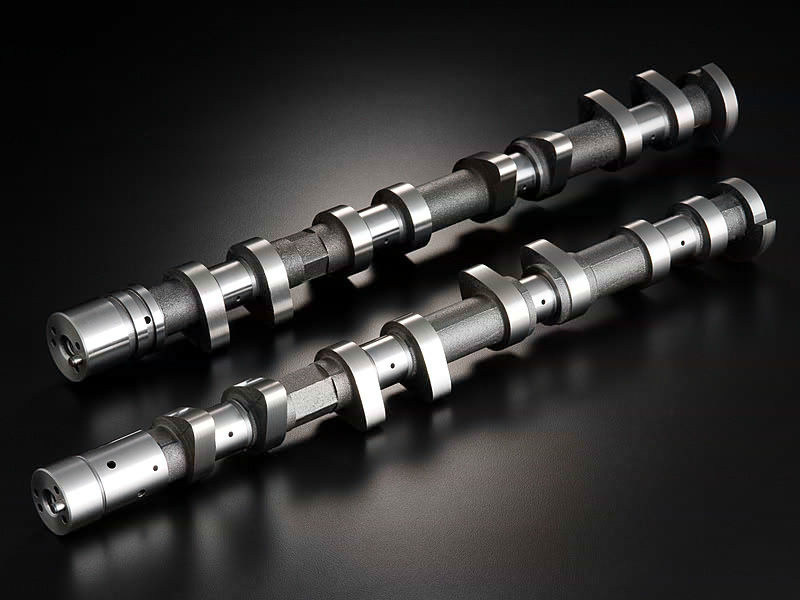
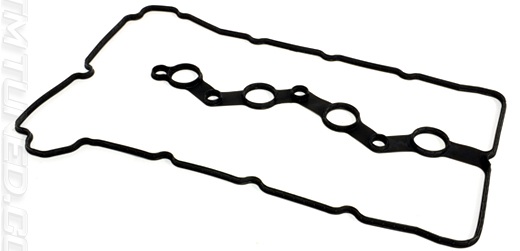
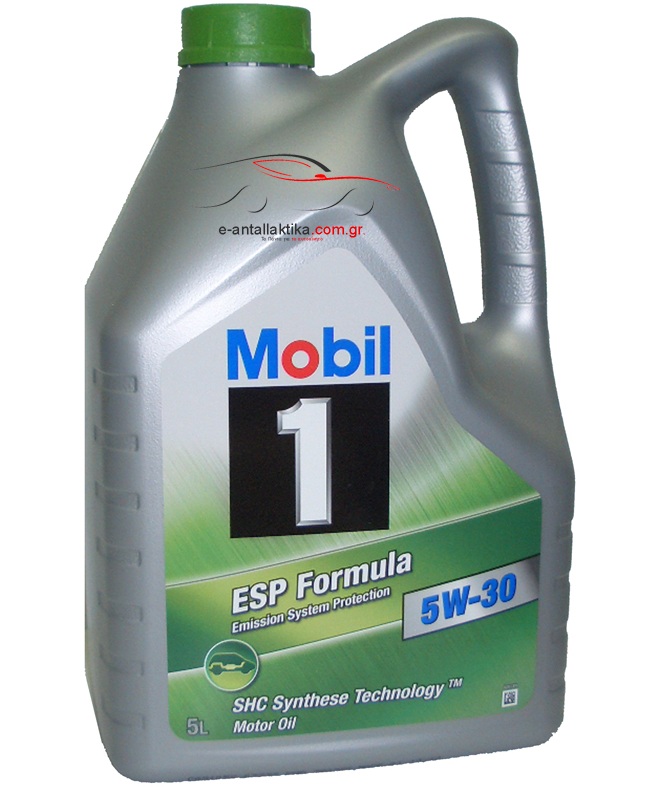
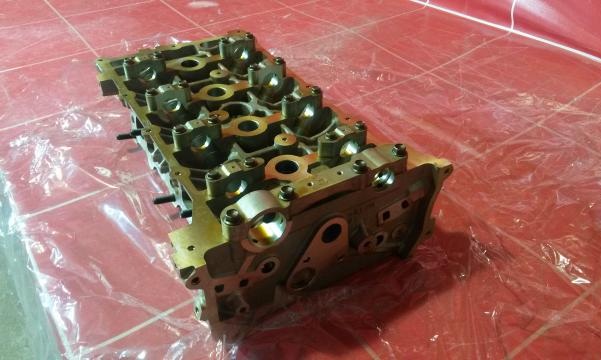
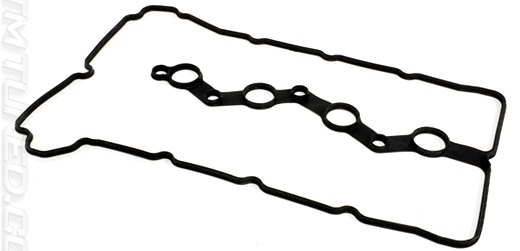
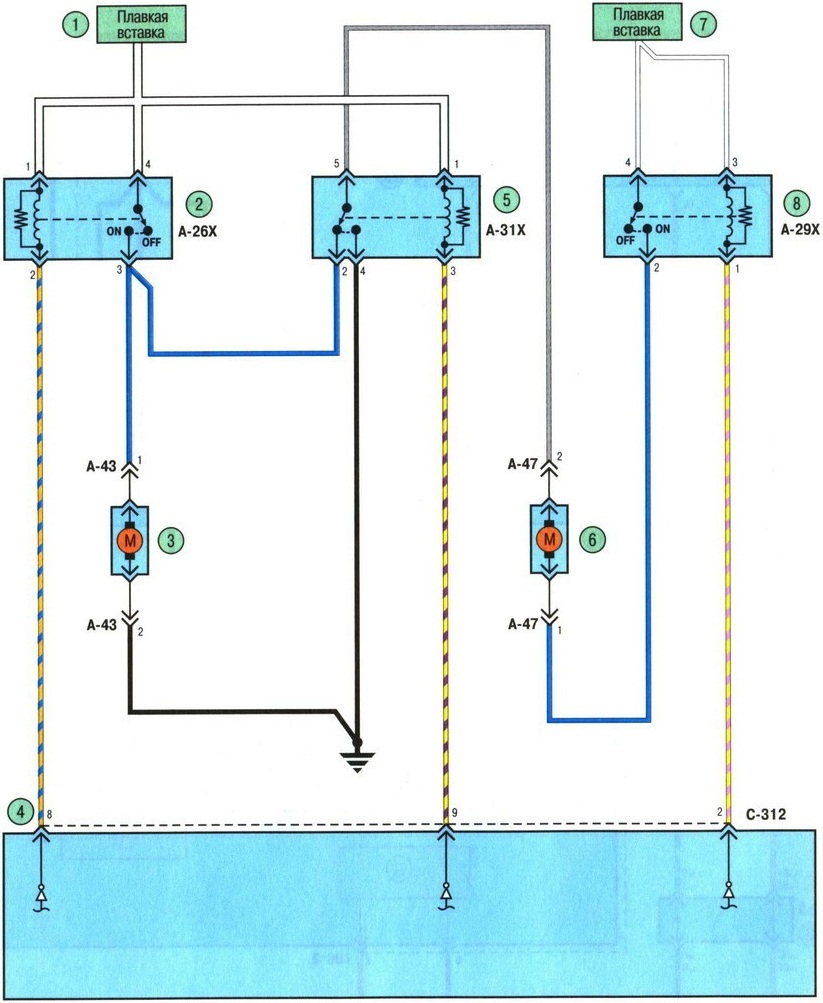
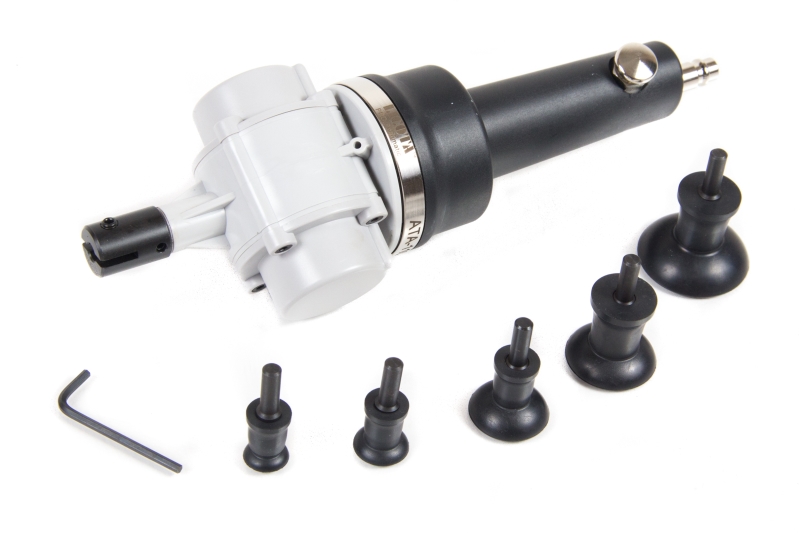